For industrial machinery to function, chains and sprockets are essential. Together, these vital mechanical parts transmit power, transform motion, and guarantee the effective operation of heavy machinery in a variety of industries. Machinery would break down more frequently, operate less efficiently, and require more maintenance if chains and sprockets weren't in good working order. They are significant in a variety of industries, including manufacturing, logistics, automotive, and agriculture. Optimising industrial performance requires an understanding of the various kinds of chains and sprockets, their uses, and the considerations that go into choosing and maintaining them.
Types of Industrial Chains and Their Applications
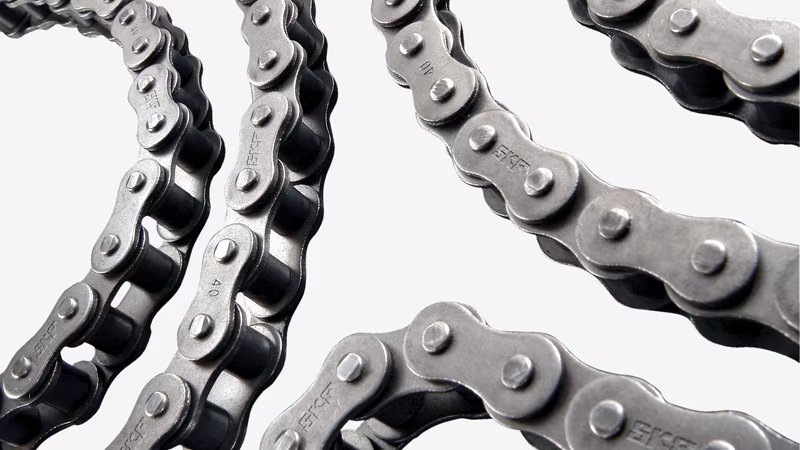
Industrial chains come in a variety of designs, each suited for specific tasks. The right chain can significantly enhance the efficiency, durability, and performance of machinery. Below are the most commonly used types of industrial chains and their applications:
- Roller Chains: In industrial settings, roller chains are most frequently utilised. They are made up of several cylindrical rollers that are connected by side links. The purpose of these chains is to transfer mechanical power from one sprocket to another. Because of their adaptability, they are perfect for a variety of uses, such as motorcycles, agricultural machinery, and conveyor systems. Roller chains reduce wear and friction while transferring power smoothly and effectively.
Roller chains are frequently used in manufacturing and food processing industries due to their dependability and simplicity of maintenance. To suit a range of loads and operating conditions, these chains come in a variety of sizes and materials. - Conveyor Chains: Conveyor chains are made especially to move large objects over long distances. They are designed for strength and durability to withstand the mechanical stress of moving materials or products, in contrast to roller chains. Conveyor chains are essential to the production lines of industries like packaging, food production, and automobile assembly. To meet particular transport requirements, these chains frequently include attachments like studs or extended pins.
Conveyor chains made of stainless steel are used in settings where cleanliness is essential to avoid contamination. Conveyor chains are essential in automated and continuous production systems due to their versatility. - Silent Chains: Inverted tooth chains, sometimes referred to as silent chains, are designed to run smoothly and silently. Instead of rollers, they use interlocking teeth, which lowers vibration and noise. Applications like precision machinery and automobile engines, where low noise levels are crucial, frequently use silent chains.
Silent chains' sturdy construction enables them to support large loads and fast speeds without compromising performance. These chains are perfect for industrial settings where keeping a peaceful workplace is essential. - Leaf Chains: The main purpose of leaf chains, which are made of interlaced metal plates, is lifting and hoisting. They are appropriate for heavy-duty equipment like hydraulic lifts, cranes, and forklifts due to their high tensile strength. In contrast to roller chains, leaf chains move by means of plates and pins rather than sprockets.
Because leaf chains are strong and can support heavy loads without buckling or breaking, they are frequently used in industries that need lifting or load-bearing capabilities.
Types of Sprockets and Their Functions
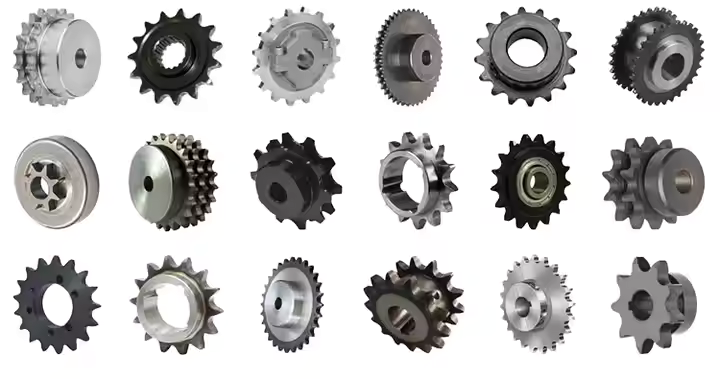
Sprockets are toothed wheels that engage with chains to transfer motion and power. The correct type of sprocket is essential for achieving optimal performance in machinery. Here are the four main types of sprockets and their functions:
- Plain Bore Sprockets: Simple in design, plain bore sprockets have a standard bore size. They work well in low-speed applications where high torque and accuracy are not essential. These sprockets are frequently found in simple conveyor systems, agricultural equipment, and other fundamental mechanical configurations. Plain bore sprockets are simple to install and replace because of their uncomplicated design. For less demanding applications where high precision is not necessary, they provide an affordable option.
- Taper Lock Sprockets: To mount firmly onto a shaft, taper lock sprockets need a separate bushing and have a tapered bore. They are perfect for heavy-duty applications because of their design, which makes installation and removal simpler. Taper lock sprockets are essential to industries like mining, steel production, and manufacturing because of their robustness and capacity to manage high torque and speed. Because these sprockets are simple to disassemble without removing other parts, they are recommended in applications requiring frequent maintenance.
- Idler Sprockets: Idler sprockets are used to guide and maintain tension in a chain system; they do not transmit power. They contribute to smooth and effective operations by preventing chain slack and misalignment. Automotive engines, conveyor systems, and other applications involving lengthy chain runs frequently use these sprockets.Idler sprockets prolong the life of the driving sprocket and the chain by preserving the right chain tension.
- Split Sprockets: Split sprockets are made to be simple to install and maintain. It is possible to replace them without disassembling the entire drive system because they can be divided into two parts. These sprockets are perfect for industrial and agricultural machinery that needs regular maintenance. They are a sensible option for heavy-duty applications where effectiveness and ease of maintenance are essential because of the split design, which lowers labour costs and downtime.
Factors to Consider When Choosing the Right Chain and Sprocket
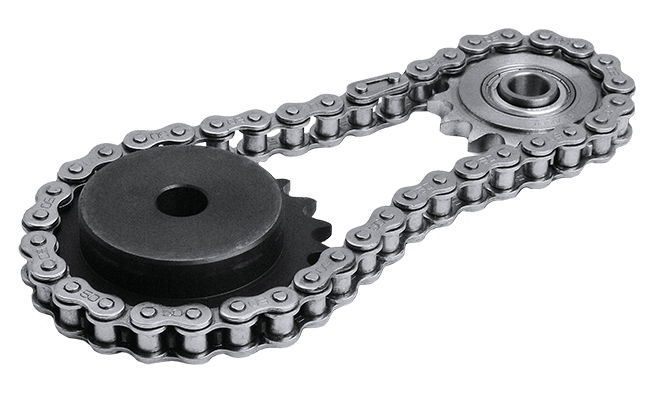
Selecting the appropriate chain and sprocket combination is vital for ensuring optimal machinery performance. Key factors to consider include:
- Load Capacity and Speed: The maximum weight that a chain can support before breaking or deforming is known as its load capacity. Because higher speeds cause more wear and friction, speed is equally important. For long-term performance, choosing a chain and sprocket that correspond with the operating load and speed is essential. Silent chains or specially treated roller chains are best suited for high-speed applications. Leaf chains or heavy-duty roller chains provide better tensile strength for heavy loads.
- Environmental Conditions: Environmental elements that affect the lifespan and functionality of chains and sprockets include temperature, humidity, and chemical exposure. While coated sprockets provide extra protection in challenging conditions, stainless steel chains are appropriate for corrosive environments. To guarantee longevity and dependable performance, the working environment must be taken into account when choosing components.
- Maintenance and Durability: Sturdy chains and sprockets lower maintenance expenses and downtime. Seek out parts with easy-to-replace designs, wear-resistant coatings, and sophisticated lubrication systems. The chain and sprocket system's lifespan is increased by routine maintenance, which includes lubrication and tension checks. Costly repairs and unplanned failures are avoided with proper maintenance procedures.
Best Practices for Chain and Sprocket Maintenance
Consistent maintenance is essential for ensuring the efficient operation of chain and sprocket systems. Follow these best practices to enhance longevity and performance:
- Lubrication: Use appropriate lubricants to minimise friction and wear. Regular lubrication reduces noise and extends the lifespan of both the chain and sprockets.
- Inspection: Conduct regular inspections to identify signs of wear, misalignment, or damage. Early detection of issues prevents more significant mechanical failures.
- Tension Adjustment: Maintain proper chain tension to prevent slack and excessive wear. Loose chains cause inefficiency, while overly tight chains accelerate wear.
- Cleaning: Remove debris and contaminants from the chain and sprockets to prevent abrasion and corrosion.
- Replacement: Replace worn chains and sprockets promptly to avoid costly breakdowns. Keep spare parts on hand to minimize downtime.
In order to ensure smooth operation and effective power transmission, chains and sprockets are essential components of industrial machinery. The performance and longevity of machinery are improved by knowing the various kinds, their uses, and how to choose the best combination. Industries can lower operating costs, increase equipment lifespan, and sustain steady productivity by adhering to best maintenance practices. Choosing and maintaining chains and sprockets correctly is essential to industrial dependability and efficiency.
For those seeking professional assistance or specialised expertise in dealing with pneumatic valves, SLSPRO stands as a reliable partner.
SLSPRO experts offer comprehensive services and provide tailored solutions and
specialised services to meet the unique needs of clients across various industries.
You can also browse our extensive
chains and sprockets selections on our website.
Get in touch with us for professional help and greater operational efficiency today!