Modern manufacturing has been transformed by robotics, which increases productivity, accuracy, and efficiency. Production lines have changed over the last few decades due to developments in robotics technology, which have increased output and speed while decreasing human error. Robots are now used in everything from electronics manufacturing to automobile assembly. In addition to increasing
operational effectiveness, this change has made it possible for businesses to satisfy growing customer demands while keeping costs down.
Rapid advancements in technology, such as artificial intelligence (AI), machine learning, and the Internet of Things (IoT), are driving the use of robotics in manufacturing. Industrial production has changed as a result of these advancements, which have made it possible for smarter, more adaptable robotic systems to operate in unison with human operators.
What Are Collaborative Robots
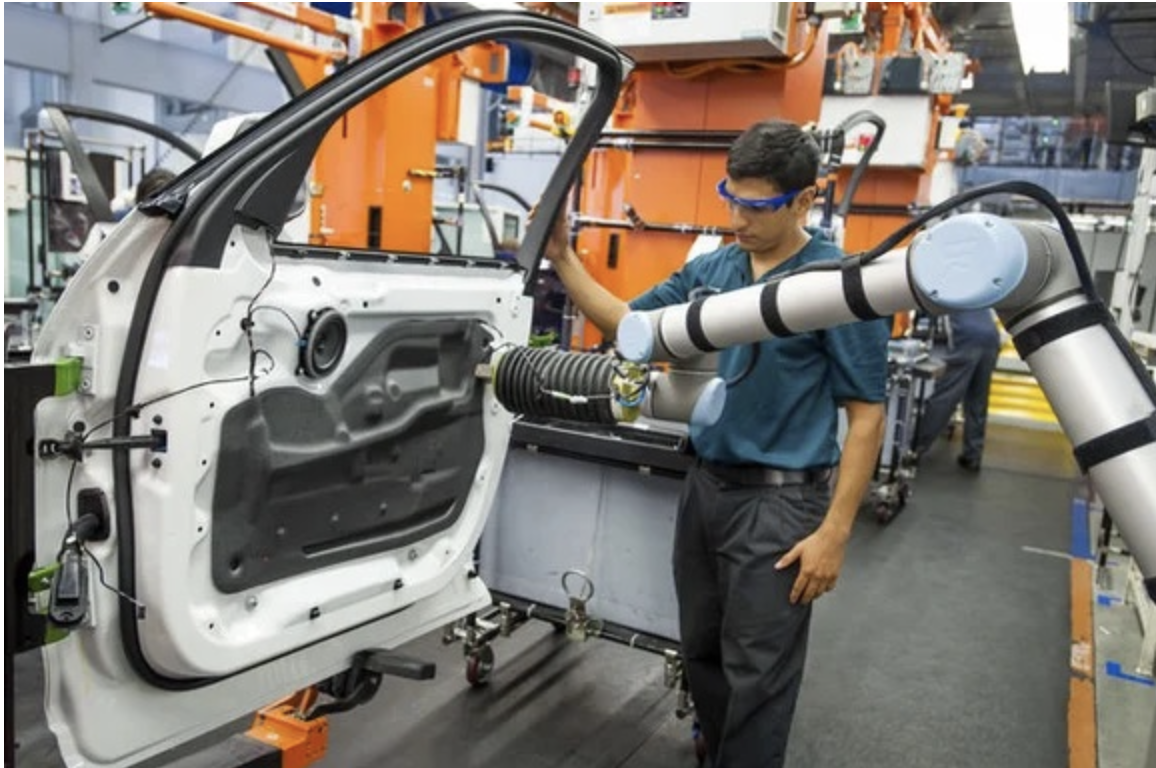
Cobots, or collaborative robotics, are machines made to work side by side with people in shared workspaces. Cobots are designed with cutting-edge safety features like force-limiting technology and real-time monitoring, in contrast to traditional industrial robots, which frequently need isolated environments. These robots help with precise tasks like putting together fragile electronics or carrying out labour-intensive but repetitive tasks.
Cobots are praised for their versatility and simplicity of programming. Cobots are especially advantageous to small and medium-sized businesses (SMEs) because they are affordable and can supplement human capabilities rather than replace them. Collaborative robotics is being used by a growing number of industries, including healthcare and automotive manufacturing, to increase productivity while preserving a safe working environment.
What Are Industrial Robots
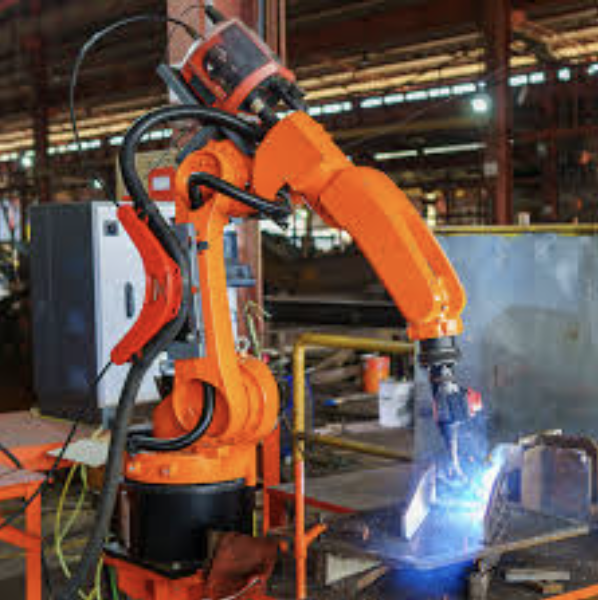
Automated systems designed to perform intricate, repetitive tasks in manufacturing settings are known as industrial robots. These robots, which are usually bigger and stronger than cobots, are used for heavy lifting, welding, and painting. They are perfect for large-scale production because they work quickly and provide precision that is greater than that of humans. Systems for industrial robotics are frequently employed in settings where dangerous conditions could endanger human workers. These systems are categorised according to their functions, such as gantry robots, articulated robots, etc. By putting them into practice, manufacturers can increase overall efficiency, decrease operational errors, and achieve greater consistency.
Key Differences Between Collaborative Robots and Industrial Robots
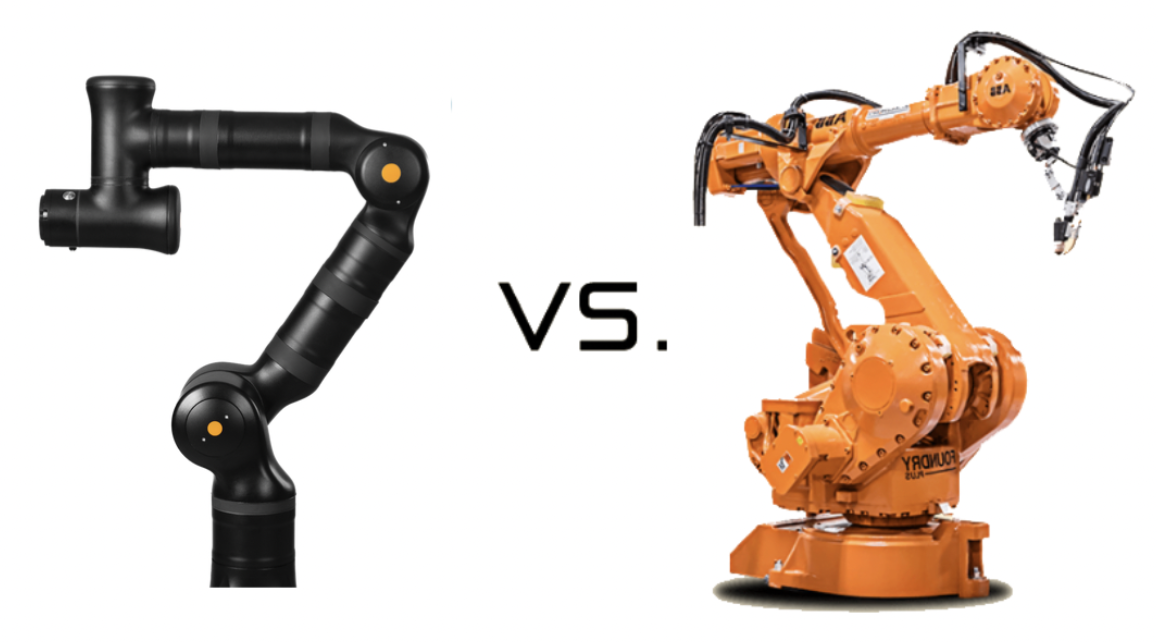
Collaborative robots and industrial robots differ primarily in their purpose and design. Safety and human-robot interaction are given top priority by collaborative robots. They have sophisticated safety features, are simple to program, and are smaller. In contrast, industrial robots prioritise power, speed, and high production volumes; therefore, physical separation is frequently necessary to guarantee worker safety. Another distinction is the degree of adaptability. Unlike industrial robots, which are usually made for specialised, repetitive tasks, cobots can be quickly reprogrammed and used for different purposes. This indicates that while industrial robotics thrives in high-output, standardised production, collaborative robotics is best suited for dynamic manufacturing environments.
- Safety and Workplace Integration: When incorporating robotics into manufacturing, safety is a top priority. Collaborative robots are safer for direct human interaction because they are equipped with features like force limitation, collision detection, and emergency stop mechanisms. Robotic safety is governed by international standards such as ISO 10218, which guarantee that industrial and collaborative robotics adhere to strict regulations. Careful planning is necessary to balance human and machine collaboration when integrating robotics into the workplace. Businesses need to assess worker preparedness, task complexity, and safety protocols. In addition to increasing productivity, effective integration shields employees from dangerous situations and repetitive strain injuries.
- Flexibility and Adaptability: Flexibility is one of the most alluring benefits of robotics in manufacturing, while adaptability is a notable characteristic of collaborative robots. They are perfect for industries that need to change production frequently because they can be swiftly reprogrammed to carry out new tasks. For large-scale manufacturing, industrial robots provide unmatched precision and consistency, despite their limited adaptability. But thanks to modular designs and more intelligent programming interfaces, technological developments are closing this gap and giving industrial robots greater flexibility. Given the rising demand for specialised and diverse products, manufacturers must be able to adapt.
- Operational Cost and Maintenance: Robotics implementation in manufacturing requires a large upfront investment. Because of their complexity, installation, and maintenance requirements, industrial robots are usually more expensive. However, by lowering labor costs and increasing production efficiency, they provide long-term savings. Conversely, collaborative robots are less expensive and require less upkeep. They lower overhead costs by requiring less infrastructure and safety barriers. Because both kinds of robotics systems reduce errors, decrease downtime, and increase productivity, they provide significant returns on investment. To guarantee optimum performance and longevity, routine maintenance and software updates are necessary.
Which Robot Type Is Right for Your Manufacturing Needs?
A number of variables, such as production volume, task complexity, and financial constraints, influence the choice of robot. For small-scale operations that need flexibility and human collaboration, collaborative robots are perfect. For SMEs looking for affordable automation to supplement human labour, they are ideal. Large-scale manufacturing, where consistency, accuracy, and speed are critical, is a better fit for industrial robots. Heavy machinery, automotive, and aerospace industries all profit from their capacity to manage difficult, repetitive jobs. The robotics solution that best suits your manufacturing processes will be determined by assessing your operational requirements and long-term objectives.
The Evolving Role of Robotics in Manufacturing

Due to market demands and technological advancements, robotics' role in manufacturing is constantly changing. Predictive maintenance, collaborative intelligence, and AI integration are examples of emerging trends. Production lines are becoming smart factories as a result of these advancements, with networked robots that maximise productivity and adjust to data in real-time. Manufacturers will depend more and more on intelligent automation as robotics technology develops in order to remain competitive. This change promises safer working conditions, lower expenses, and increased productivity. Human-machine cooperation will result in previously unheard-of industrial capabilities in the ongoing innovation of robotics in manufacturing.
For those seeking professional assistance or specialised expertise in dealing with pneumatic valves, SLSPRO stands as a reliable partner.
SLSPRO experts offer comprehensive services and provide tailored solutions and
specialised services to meet the unique needs of clients across various industries. You can also browse our extensive
cobots selections on our website.
Get in touch with us for professional help and greater operational efficiency today!